DIGITAL TWINS IN MINERAL PROCESSING
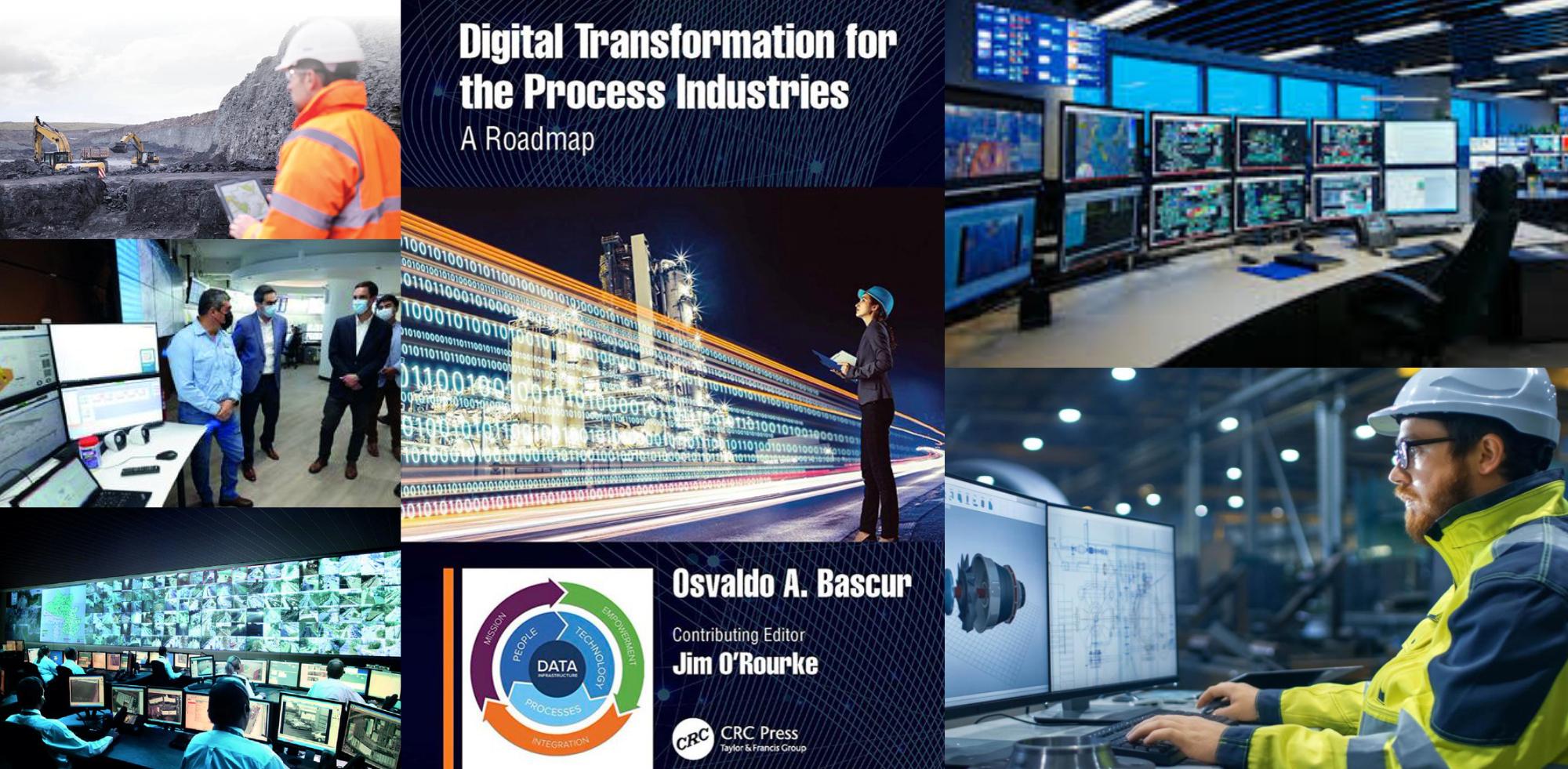
Mineral deposits are becoming extremely variable with mineralogy, hardness disturbing grinding and flotation circuits. Sensors in mineral processing plants provide large amounts of data for process optimization. The proper context and the operational events allow increased awareness for proactive actions to improve the performance of crushing, grinding, flotation and thickening / filtration circuits. A data-driven strategy is required to enable operations, maintenance, and personnel to quickly and easily take corrective action when abnormal conditions occur. A digital template transforms data into operational information in real time. This allows you to discover hidden, idle, and downtime losses using a canonical Unit strategy to model the plant. By measuring, managing these downtimes, people find new ways that prevent them fromimproving plant profitability. The inFORMation created by real-time analysis allows you to calculate recovery in real time and develop predictive analysis models to find the best operating condition based on the type of ore. It enables the creation of new workflows and collaboration between the mining, concentrator plant, and the company, including service providers. Currently remote operations support can integrate mining operations from drilling to product delivery. People can work remotely supporting operations and staying safe and healthy. Today’s companies can increase productivity by developing predictive models to detect hidden losses in production, energy and water from equipment, ore type, and unmeasured disturbances. People call this strategy tracking money losses in order to survive.
TECHNICAL FOUNDATION
Environmental restrictions and low grades require a new approach to the operational management of mining companies and their remote operations. These low grades bring a lot of variability that cause losses that are very difficult to discern in a timely manner. The speed of computers and networks creates a new opportunity to proactively configure systems to avoid operational losses. Control systems require a new type of support to maximize recovery and reduce energy, water, and reagent costs. Renew and maintain process control loops to be able to automatically execute production plans synchronizing the mine and operations. The creation of predictive models to avoid losses in production, energy, water, and environmental pollution is becoming increasingly imperative. Work remotely for real-time operational analysis, with timely alerts when approaching restrictions or leaving the optimal production bands contained in the history of effective production. Now more than ever, the remote work strategy contributes to the development of new forms of value creation in operational management.
GENERAL AND SPECIFIC OBJECTIVES
The course aims to present the great opportunities that exist in the mining industry for the integration of data from mining dispatch systems, process control, laboratory, climate monitoring and planning information mining and geo metallurgical available. Attendees will be trained in how to transform data into information for operational management. Classification, flotation, and thickening grinding models will be shown that provide the knowledge for their analysis with operational data. Examples of industrial cases will be shown. It is suggested that attendees have the plant process diagrams so that their modeling in blocks for their management.
METHODOLOGY
Process diagrams in PowerPoint will be used to show the concepts and methodology. Practical examples are shown using a dynamic simulator running in a historian to analyze the data and its transformation into information for the process model. Examples.
PPROGRAM AND CONTENT
The course content is based on the Process Control and Operational Management Chapter in the Mineral Processing and Extractive Metallurgy Manual published by the SME in February 2019. The chapters of Measuring, Managing, and transforming data into actionable information published in Smart will be used Manufacturing Concepts and Methods by Elsevier and the book Digital Transformation in the Process Industries: A Road Map published by CRC Press all available at https://www.amazon.com/-/e/B07XV5HXX9.
PARTICIPANTS
Process Engineers, Mining Engineers, Plant Managers, Technical Support, Students of Chemical, Metallurgical, Electrical, Environmental Engineering, etc.
PROGRAM
MODULE 1
The secrets of digital transformation.
Process Control and Dynamic Management of Operations.
Sensors, Control Loops and Decision-Making Strategies.
The 4 stages of value creation.
Cloud based strategies using PI System and Seeq Advanced Analytics.
Digital Twin Plant Model – Steps 1 and Step 2.
Operational states, ore types, work teams, production planning and environmental constraints.
Analysis of the global effectiveness of production.
Net Metal Production Rate, Recovery and Metal Losses.
Questions and discussion Module 1.
MODULE 2
Steps 3 Predictive Process Models.
Machine Learning integrated Data Cleansing and Event Classification.
Hybrid Grinding Classification Dynamic Models.
Hybrid Flotation Dynamic Models.
Hybrid Water Recovery Thickener Models.
MODULE 3
Pyrometallurgy Smelter and Refining Examples.
Hydrometallurgical Process Models and Examples.
Advanced Monitoring of Process Control Systems.
Predictive Models for Critical Equipment.
External Remote Support.
Questions and discussion Module 3.
MODULE 4
Digital Transformation Step 4.
Operational Integration Mines, Plants and Dispatches.
Net Copper Production and Recovery Maximization.
Operational Center of Mine Plants.
Production, Energy and Water Operational Center.
Center for Monitoring and Diag.
Questions and discussion Module 4.
Conclusions and Closure of the Course.
Final evaluation.
EXPERT INSTRUCTOR : Dr. OSVALDO A. BASCUR
Principal Digital Transformation – OSB Digital, LLC in Houston, TX.
Dr. Bascur is currently Principal Digital Transformation at OSB Digit, LLC and he is Consultant Fellow for Seeq Advanced Analytics. He worked as a principal at OSISOFT for 25 years. He was a staff engineer for Pennzoil and before he was process control engineer working for Duval Corporation, Tucson, Az (now Freeport McMoRan).
He has recently designed a template for the digital transformation of Plants for dynamic operational management, quality, asset and energy/water optimization. Today, the Digital Plant Strategy transform sensor data into Operational Insights (Data + Operational Events) to enable Overall Production Effectiveness and Predictive Analytics. The strategy identifies the Hidden Production/Energy/Water Losses in an Industrial Plant enabling Production Maximization while eliminating losses. This template strategy enables the transformation of huge amounts of unusable data into InFORMation to generate additional Operating Insights, Predictive Models, and integrates with Business Intelligence Tools such as MS PowerBI, Seeq Advanced Analytics, and AWS Quick sight.
Dr. Bascur wrote the chapter on Process Control and Operational Intelligence for the SME Mineral and Extractive Metallurgy Processing Handbook in 2019. He contributed with a chapter Measuring, Managing and Transforming Data for Operational Insights for the Smart Manufacturing Concepts and Methods led by the University of Texas and Drexel University. He edited the Latin American Mining Perspectives: Exploration, Mining and Processing for the SME. In addition, he has written more than 95 technical papers and contributed to numerous chapters in several books. He is editor of the MEI and IFAC publications.
He received the most prestigious SME Antoine Gaudin Award in 2014. He is a member of the AIChE, SME, AIST, IFAC MMM and the IMPC.
He is a Chemical Engineer and Metallurgical Engineer from the University of Concepción. He received his PhD in Metallurgical Engineering from the University of Utah, Salt Lake City, USA.